
Your reliable process starts with our plastic components.
Our services
From design to validation, Plast4Life is here to support you with clean injection molding services.
-
It all begins with an idea. We can shape it into a real and scalable project: from application-based plastics selection and support of the design to the fast-track prototyping and pilot manufacturing of your plastic tools and components for life science use.
-
Mold development is central for every new injection molding project. We numerically analyze the melted polymer flow, injection pressure, and clamping force required for the production your plastic parts. All to deliver reproducible, safely and efficient manufacturing process.
-
Our injection molding machines go from 6 to >250 tons of clamping force. Our aim is to propose different background cleanness depending on the needs of your applications:
• ISO 8 for standard productions;
• ISO 7 for clean productions;
• ISO 5 for the most demanding applications in terms of cleanness.
The automation technologies and controls allow maximal reproducibility and minimized human presence.
-
Life science requirements are by nature one of the highest. We offer uppermost quality standards based on validated processes and our Quality Management system. Post production operations as for instance, assembly or clean protective packaging, are additional projects we will be keen to discuss with you.
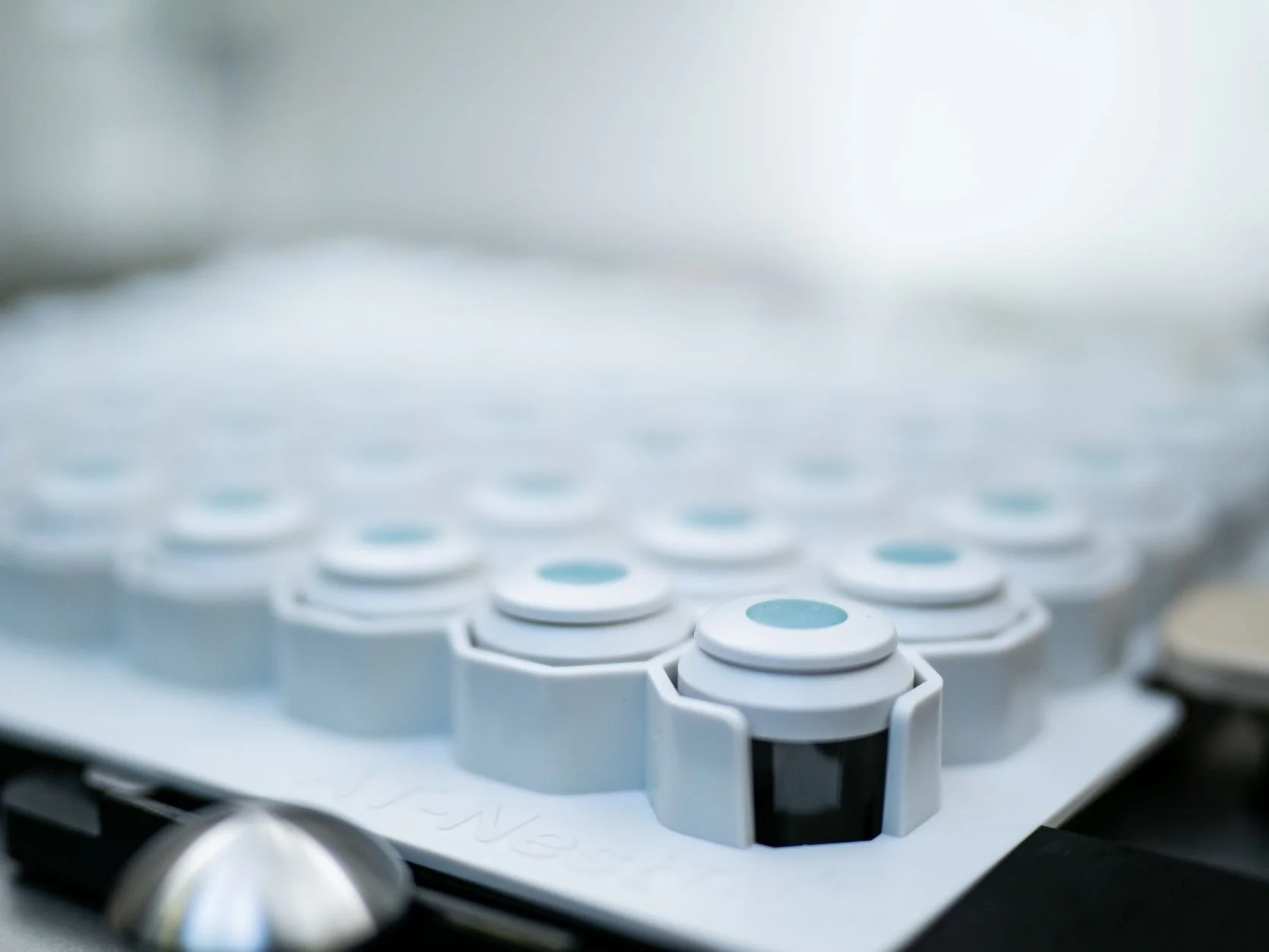
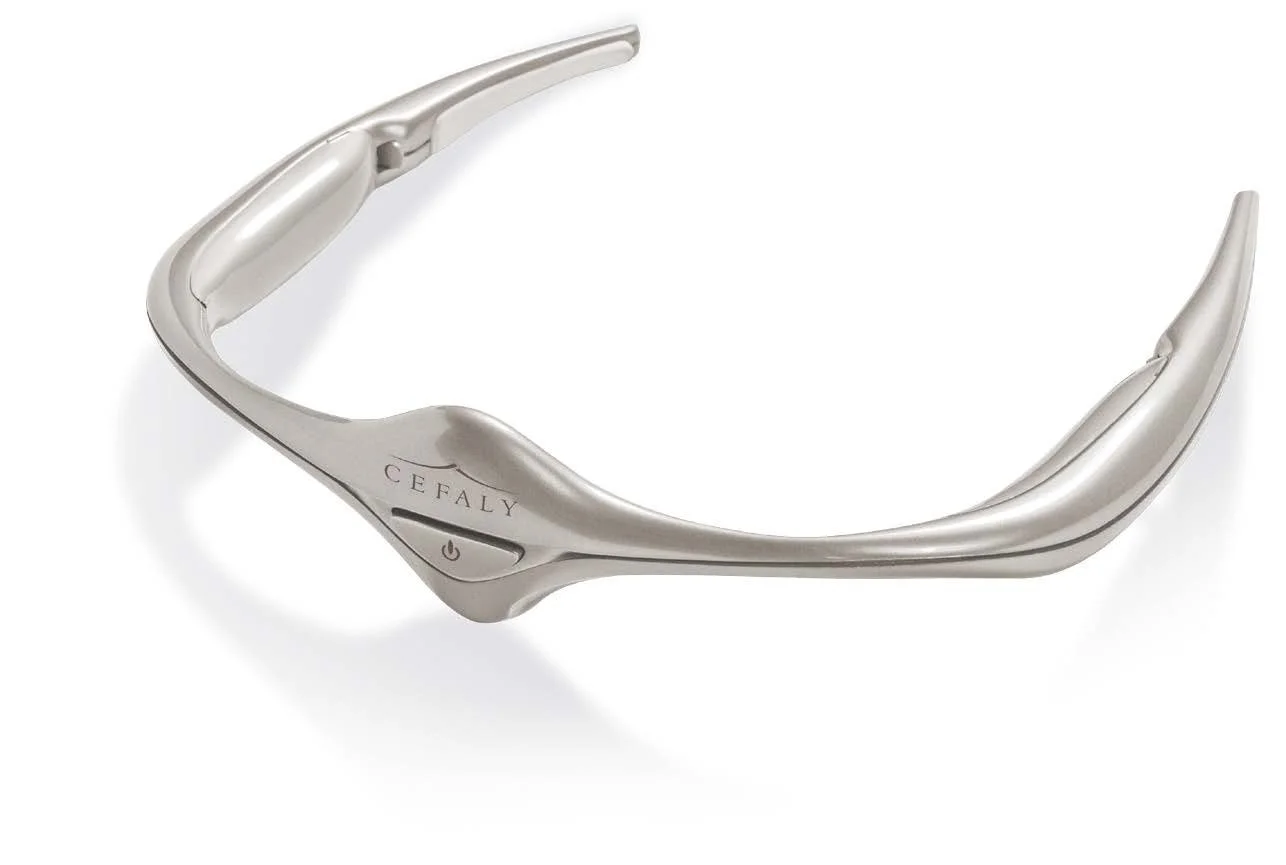
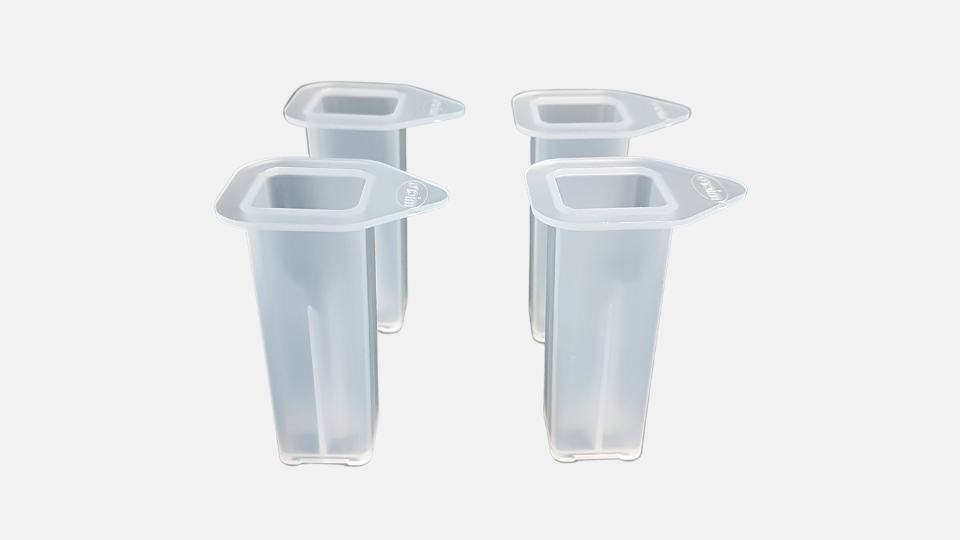

Advantages of injection molding
Design flexibility
Scalability and high-throughput readiness
Wide plastic choice for various needs
Wide color choice
Product consistency
Low rejection rate and low plastic waste
What is ISO 7 environment?
ISO 7 cleanroom environment are used in various industries to protect the contained process from contamination with particles of dust, hair, paper etc. Such environment shall achieve less than 352,000 of smallest (≥0.5 μm) particles per cubic meter. Such levels of cleanliness are achieved by design, special procedures and the HEPA filtration. At Plast4Life we maintain ISO 7 conditions to achieve high purity standards for our injection molding products.